The concept of 'circularity,' 'circular economy,' and similar "buzzwords" have gained traction in the world of plastics packaging as multi-national brands undertake initiatives to do their part in tackling waste management from single-use packaging, pledging to make all of their packaging reusable, recyclable or compostable by 2025.
When examining what the term "circular economy" really means and what that would look like in our modern society, maybe it's easier to first examine what it's not. Our current production economy is linear in that material is obtained from natural resources, products are produced and - in the majority of cases - those products are thrown away, i.e. take-make-waste. A circular economy, by comparison, aims to significantly reduce or eliminate waste by planning for a product's end-of-life, and strives to recapture waste as a resource for reuse back into the production process, i.e. take-make-reuse. Per the Ellen MacArthur Foundation's definition, a circular economy is based on three principals:
-
- Eliminate waste & pollution
- Circulate products & materials
- Regenerate nature
Ultimately, the ability to achieve this is rooted in design or redesign - a topic that we discussed in our previous post in this series focused on the "reduce" component of the 'Three R's,' in which we argued that a fourth "R," for redesign, was necessary considering circular economy and waste reduction goals. When it comes to how the concept of how a "Fourth R" comes into play regarding the topic of reuse, the key is to redesign materials that, given existing infrastructure, material components and chemical makeup, are capable of being reused back into new products.
Keeping the 2025 goal in mind, organizations such as the U.S. Plastics Pact (the "U.S. Pact"), have been developed to "unify stakeholders across the entire plastics value chain to rethink the way we design, use, and reuse plastics, ultimately reducing plastic waste in our environment and creating a circular economy for plastics," and help the industry achieve their ambitious goals, even going so far as to establish a "Roadmap to 2025" defined by four key milestones:
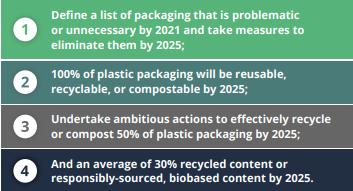
*Image source: U.S. Plastics Pact Roadmap to 2025: Executive Summary
Steps 1 and 2 are firmly dependent on packaging redesign with recycling (step 3) and reuse (step 4) in mind, emphasizing how important the relationship between redesign and reuse is to achieving industry-wide goals in that one cannot be achieved without the other.
As a producer of plastic packaging materials for the food packaging industry, ICPG is committed to helping brands and converters redesign products in a way that helps them achieve their internal objectives while fulfilling their commitments to contribute to the broader goal of a circular economy. So when it comes to redesigning food packaging with the goal of reuse in mind, what is important to consider? In the second post of this three part series, we continue the process of taking the steps to rethink considerations for eco-conscious material selection as it pertains to the "Three R's", and next up is reuse.
Design & Redesign for Reuse
As mentioned above, a key component to reuse is the design & redesign of packaging solutions keeping circularity goals in mind. But designing for reuse can actually have multiple meanings. In recent years the market for reusable packaging, i.e. packaging that is designed to be used multiple times rather than single use, has grown. According to market research firm Mintel, the market for reusable beauty and personal care products grew by ~65% from June, 2020 to May, 2021, and global corporations in the food & beverage space have tested reusable packaging programs within the last few years.
While the overall intention is to reduce the carbon footprint of the packaging solution by extending its usable life and reduce waste, this is dependent on the consumer to use the packaging as intended. Packaging produced for this purpose is often produced with a more durable material such as metal or glass, but that may actually have broader implications on the overall carbon footprint of the solution due to the increased weight - which, if the consumer does not actually reuse the packaging and disposes it as it it were intended for single-use, just results in wasted resources. So while well-meaning, some of these reusable items never reach their "payback" period, discussed in Time's article "Reusable Packaging Is the Latest Eco-Friendly Trend. But Does It Actually Make a Difference?," which refers to the amount of times a reusable item must be reused before it is actually better for the environment than its single-use counterpart.
But all is not lost on the single-use side of the equation. Another way to accomplish this is to design packaging materials in a way that allows materials to become a resource at the end of a products usable life and circulated back into the manufacturing of new products. For plastic packaging applications, this requires careful attention to whether or not the materials, or mix or materials, can be reused and under what circumstances. Consideration of a few key factors impacting packaging reusability include:- Material complexity:
The primary function of packaging materials designed for food packaging is to keep the contents safe until it reaches the consumer. This doesn't just include bumps and bruises that may occur along the supply chain - it also includes protecting the food product from the impact of environmental factors such as oxygen, moisture and even for some products, UV rays - which can lead to spoilage. Each year billions of dollars are lost due to food spoilage at the retail level. Outside of this financial impact, there are also environmental costs associated with food waste and waste to landfill. Modifying packaging design through the use of innovative materials to extend shelf-life by just one day can help recover a significant portion of that waste and the cost associated with it - so protecting the product is a key concern from a financial and environmental perspective.
Typical packaging materials naturally possess an inherent level of protection from oxygen and moisture, which depending on the food product and retail storage conditions, may be sufficient to maintain the integrity of the product through its sell-by date. However, shelf-stable and extended shelf-life products typically require the use of specialty barrier materials such as EVOH or PVDC in combination with a base polymer such as PP, PS or PET in a multi-layer coextruded rollstock structure to achieve the required barrier protection.
While the resulting multi-layer structure will provide adequate, if not more, barrier protection to keep the food product safe through it's target shelf-life, it can pose a challenge from a recycling perspective because of the mix of materials and inability to separate those materials for diversion into separate recycling streams. Ever heard of the term "monstrous hybrid"? The term, coined by Michael Braungart and William McDonough, creators of the Cradle to Cradle® design principles developed in the 1990s, refers to a "product, component, or material that combines both technical and organic nutrients (such as recyclable paper and poly-vinyl-chloride) in a way that cannot be easily separated, thereby rendering it unable to be recycled or reused be either system." (Definition via Sustainability Dictionary) A couple additional examples of this include common barrier food packaging structures such as PET/EVOH or HIPS/PVDC, which due to the inability to separate these materials means that they are not recyclable through existing recycling streams and will therefore not be diverted for reuse, thus emphasizing the important part that material selection plays in designing for reuse.
However, not all multi-layer structures using barrier materials are "monstrous hybrids." Certain materials, because of their chemical makeup, even when combined in a multilayer structure do not impact the recyclability of the material. This claim was tested in a study commissioned by RecyClass, an organization dedicated to advancing plastic packaging recyclability, and ensuring traceability and transparency of recycled plastic content in Europe. The objective of the study was to test the compatibility of EVOH barrier in polypropylene (PP) rigid packaging in recycling processes and the test was performed on both a PP bottle consisting of 6% EVOH and a 3% polypropylene-grafted maleic anhydride (PP-g-MAH, with MAH > 0.1%) tie layer and a PP Sheet of the same makeup. Findings of the study proved that a concentration of up to 6% of EVOH tied with PP grafted maleic anhydride did not have a negative impact of the polypropylene materials and were fully compatible with the recycling stream. However, the same structure with concentrations higher than 6% of EVOH was found to have limited recycling compatibility, emphasizing that it is not just the combination, but also the ratio of those materials must be considered when designing for reuse. - Eliminate problematic materials:
While we're talking about monstrous hybrids, cue the U.S. Plastics Pact Roadmap to 2025 milestone #1. The U.S. Plastics pact defines problematic or unnecessary materials as: "Plastic packaging items, components, or materials where consumption could be avoided through elimination, reuse or replacement and items that, post-consumption, commonly do not enter the recycling and/or composting systems, or where they do, are detrimental to the recycling or composting system due to their format, composition, or size."
In early 2022, the U.S. Pact released said list, identifying a number of materials that it deemed to fit the above criteria. The 11 items on the list include some common materials used in shelf-stable and refrigerated rigid food packaging including: Opaque or pigmented PET, PS, PVC and PVDC, as these materials were deemed to not currently be reusable, recyclable, or compostable with existing U.S. infrastructure at scale, nor are these materials projected to be kept in a closed loop in practice and at scale by 2025. A couple of these materials, namely opaque PET & PS, may seem surprising given their prevalence in the packaging market and discussions about use of post-consumer recycled (PCR) materials in the form of rPET and rPS.
Which brings us to our third consideration for material selection... - Material Recyclability:
A key word to note in U.S. Pact's definition is "at scale," which refers to the ability of a material to be recycled not just in theory but in practice, and at a level that is meaningful enough to warrant a market for the materials because, ultimately, recycling is a business. According to the World Economic Forum, a mere 14% of plastic packaging is recycled globally. In fact, even for the well meaning consumer, I hate to have to be the one to tell you that some of the plastic, glass and cardboard that you do recycle ultimately ends up as waste anyway for varying reasons from contamination, to inconsistent recycling practices, to MRF infrastructure limitations - but we'll save that for another blog post.
Recycling processes are complex, and evaluating material recyclability in practice & at scale is an important consideration for circular economy goals because technically recyclable only gets you so far - what matters more is if it will actually be recycled. For PET/rPET, this is because the majority of the reclamation stream is dedicated to clear PET - think water bottles - which represents a valuable and robust recycling stream contributing the diversion & reuse of millions and millions of clear plastic water bottles. Because the recycling stream is so dominated by clear materials, the addition of opaque materials would contaminate the recycling stream. In addition, many food products contaminate PET packaging beyond the ability to be recycled.
When it comes to rigid PS, recycled PS is currently being evaluated for reuse through a mechanical recycling process - the issue here is once again, scale. If the material is not collected at scale, and is not expected to be, then collecting the material for reuse in mechanical recycling or otherwise will prove difficult and challenging to implement programs using recycled PS in practice.
Turns out that, when it comes to designing plastic packaging for reuse, the Three R's actually had the order - reduce, reuse, recycle - wrong the whole time. If the goal is reuse in remanufacturing, a more logical way of thinking, to ensure that reuse is an option is to consider the recyclability of a material earlier - "reduce, recycle, reuse."
Recycling Impacts Reuse
After all this effort to design packaging for reuse in the manufacture of new products with the ultimate goal of waste reduction - key in closing the loop is gaining access to these materials in a safe and efficient manner. New technologies bringing to market advanced recycling PP purification processes and investments in recycling infrastructure are making this a possibility and taking us one step closer to enabling the use of PCR materials in a variety of packaging applications, including food. Stay tuned for the next blog in our "Three R's" series to learn more about key recycling considerations to improve the sustainability of your food packaging, including the use of PCR materials.
To learn more about how you can reduce your environmental packaging solution check out ICPG's sustainable material replacement solutions for thermoformed and form-fill-seal food packaging: